
Timber Frame Construction
Timber frame construction consists of panels of timber studwork. At its most basic, a timber frame structure features walls consisting of timber studwork fixed in place (typically) with oriented strand board (OSB) or plywood. The strength and rigidity is supplied by the board, which, when nailed to the studwork, makes a very rigid box known as an open panel — the panel is ‘closed’ once insulation has been introduced.
The frame is wrapped on the outside with a waterproof barrier and then wrapped around this are the external wall elements, which can be either built up out of the ground (brick or stone), or hung off the timber frame walls — as would happen with timber cladding or tiles.
In terms of ease of build, timber frame tends to work best with simpler-shaped

Closed Panel System
structures and it really comes into its own when combined with lightweight wall claddings such as timber, tiles or render on boarding. This can reduce wall widths by up to 150mm, which adds a sizeable amount to internal floor areas.
Timber frame homes can be built on site (known as a ‘stick’ build), but the UK’s self-build timber framing industry is based around off-site construction — the timber frame panels are prefabricated in a factory and rapidly assembled on site.
Factory prefabrication is by far the most popular route chosen by self-builders, as manufacturers have to work to strict quality control methods, ensuring the correct specification of materials are used and a high degree of dimensional accuracy is achieved.
There are two main types of timber frame — open panel construction and closed panel construction.
Open panels - are manufactured ready for external joinery (doors and windows) to be placed, and are delivered to site together with flooring elements and roof trusses. The panels are delivered without insulation or vapour control layers in an open format, hence the name. Once the building is weather tight and the electrical and plumbing carcassing has been completed, the insulation can then be installed between the studs before a vapour-proof barrier is tacked up, followed by the internal lining with plasterboard
Closed panels - are delivered to site with insulation already factory fitted. The external cladding, windows and doors may be fixed, as may electrics and plumbing. Alternatively, a service void may be added for self builders undecided on their electrical and plumbing scheme. The service void within the panels provides convenient access for the plumber and electrician to carry out their 1st fix which will also reduce their time on site and their costs. Not only this, but the service void also provides improved thermal performance to the panels.

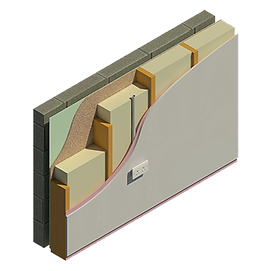
Open Panel System
Closed Panel System
A basic timber frame package may typically consist of the following items :-
-
Sole-plates, damp-proof courses and clips;
-
Structural external/internal wall panels and waterproof membrane;
-
Floor joists and floor covers (not finishes);
-
All roof elements, usually supplied as prefabricated trusses.
Items that are unlikely to be included unless the whole housebuilding contract is let to the timber frame company, or the main contractor :-
-
External claddings;
-
Roofing materials: felt, batten, roof tiles, etc.;
-
Insulation;
-
Floor screeds;
-
Chimney flues;
-
Glazing (though joinery is increasingly being supplied pre-glazed);
-
Heating, plumbing and electrics;
-
Plaster finishes;
-
Kitchen units, fitted bedroom furniture and sanitary-ware;
-
Decorating, wall and floor tiling and finishes;
-
Garage doors.
Many package companies will not manage the groundworks, drainage and landscaping. However, a main contractor will manage all of these aspects of the build..
The advantages of a manufactured timber frame system are :-
-
Speedy on-site construction – standard houses can be complete in 8-12 weeks;
-
Ideal for creating open plans;
-
Excellent insulation levels with thinner walls than masonry.
The disadvantages are :-
-
Frame fabricated off-site, with lead times of 4-8 weeks;
-
Foundations must be perfectly level within small tolerances;
-
Little scope for modification of frame after fabrication